CERN, GSI, POLITO and POLIMI carry out an extensive characterization campaign of a broad range of advanced materials for applications in future particle accelerators, as well as high-technology industrial domains. The collaboration characterized both novel materials, currently under development, as well as commercially available carbon-based materials, including thin-film coatings. This work has been developed in the context of the H2020 project ARIES.
The development and use of high thermal performance materials, with low mass density and excellent resistance to thermal shocks, is increasingly becoming an enabling technology in a broad range of industrial and research applications.
In industry, these materials are appealing in a number of fields, such as high power electronics, avionics, energy production, aerospace, nuclear engineering, and luxury sports automotive. Researchers and engineers working in these domains require materials with efficient thermal management, high temperature resistance and mechanical robustness. In the field of fundamental research, some components of the high-energy particle accelerators largely share these requirements. In fact, beam-intercepting devices (BID), such as collimators, beam absorbers, catchers, dumps and targets, are routinely exposed to the impact of highly energetic and intense particle beams, making the selection of key materials extremely important.
This is especially true for the next-generation of accelerator facilities like the High-Luminosity upgrade of LHC (HL-LHC) at CERN, the Facility for Antiproton and Ion Research (FAIR) at GSI, or the proposed Future Circular Collider (FCC). They will exhibit increased beam intensities (in some cases by orders of magnitude). In combination with the shorter pulse lengths and greater particle densities requested by physics experiments, this leads to significantly higher transient thermo-mechanical loads in all beam-intercepting devices. Additionally, materials for some of these components must possess high electric conductivity to limit the destabilizing effects they may induce on particle beams circulating in their close vicinity.
Unfortunately, no existing material possesses the combination of physical, thermal, electrical and mechanical properties, imposed by such extreme working conditions. For instance, the material currently employed for the absorbers of LHC Collimator jaws (a two-dimensional carbon-fibre-reinforced carbon composite – CFC – ) is predicted not to satisfy the full set of requirements imposed by the severe working conditions expected in the HL-LHC from 2026. In particular, numerical simulations indicate that the limited electrical conductivity of CFC may induce electro-magnetic instabilities in the particle beam.
In recent years, CERN has collaborated with international laboratories, universities and industries to address these issues. After having commenced in the framework of EuCARD and EuCARD-2 projects, this partnership is continuing within H2020 ARIES collaboration, Work Package 17 (PowerMat), a Joint Research Activity, in cooperation with Work Package 14 (Promoting Innovation).
Carbon-based materials have a long history of applications in beam intercepting devices and their harsh radiation environments, thanks to their low activation, high radiation-hardness, thermal stability in combination with improved strength at high temperatures and low density. PowerMat focuses on the exploration of advanced types of carbons, such as various grades of isotropic graphite, thermal pyrolytic graphite, CFC and carbon foams. It has also targeted the development of novel composite materials based on the combination of graphite and diamond with metals or high performance ceramics.
In this context, a family of new graphite-matrix composites, reinforced with molybdenum carbides (Molybdenum Carbide – Graphite, MoGr) has been co-developed by CERN and Brevetti Bizz, an Italian SME, with the goal of increasing the electrical conductivity of the materials for the primary and secondary collimator jaws, while maintaining or improving the beam impact robustness of CFC. To further enhance the electrical conductivity of the jaw surface exposed to the beam, a thin film of electrically conductive metals or ceramics can be applied to the MoGr bulk material. Solutions under development are, for example, molybdenum, copper and titanium nitride coatings.
In order to assess the performance of these materials and gain a deeper understanding of their response to beam-induced dynamic thermal shocks, dedicated experiments are carried out at facilities like CERN’s High-Radiation to Materials (HiRadMat), GSI’s UNILAC and SIS 18 accelerators, with short-pulse, high-intensity beams.
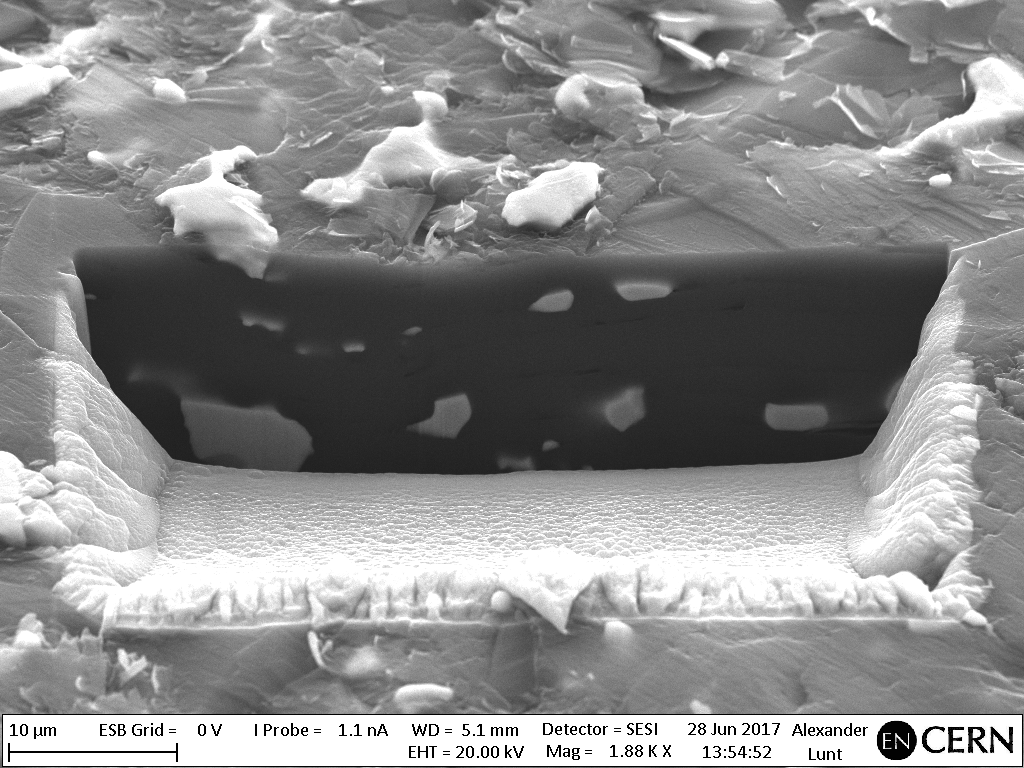
Figure 2. (CERN)
WP17 partners have performed an extensive characterization of both commercially available advanced materials and newly developed composites. The characterization performed included the study of materials morphology and microstructure, the measurement of their thermal, electrical and mechanical properties, as well as their behaviour in ultra-high vacuum, and the study of application of thin films on the surfaces of the bulk materials. This campaign has allowed quantifying the advantages of novel composites, compared to commercial materials and has laid the ground for further optimizations and improvements in the development of advanced thermal management materials. It will be complemented in the course of the projects by additional characterization campaigns, including examination after long-term irradiation and experiments under high intensity particle pulses.
During the course of this work, the ARIES Consortium also plans to engage experts from space, aviation, car and electronic industry to exchange ideas on the latest developments in design, manufacture, testing and applications of novel thermal management materials. These industries could consider the novel materials developed in this WP for advanced engineering solutions, efficient energy solutions and thermal management, given their excellent thermal conductivity and high mechanical and shock resistance.